Business London Magazine – March 2007
By Kim Wolfe
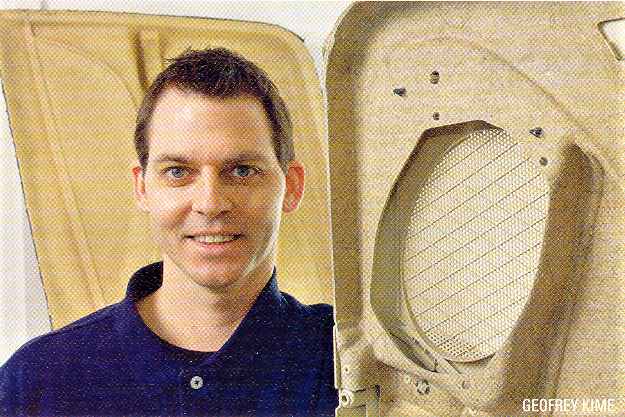
When Geofrey Kime and Joe Strobel broke ground to plant hemp seeds in 1994, they also broke a 50-year prohibition on hemp cultivation in Canada. Production of industrial hemp was banned at the end of the Second World War because of the plant’s resemblance to its THC-laden cannabis cousin.
“It was a case of mistaken identity” explains Kime. “We were granted the first licence to grow industrial hemp in modern times. The plants we grew did not contain narcotics.”
Kime no longer grows his own crops, but he continues to be a pioneer in the field of hemp and it’s industrial uses. Kime is the president of Stemergy (formerly Hempline Inc.), a Delaware, Ontario based company that produces bio-fibres from hemp and other annual stem fibre plants such as flax. The company is privately held, and Kime remains one of the key owners.
“We are one of the only companies running a hemp and flax fibre extraction and refining facility in North America” say Kime, adding that Stemergy sources hemp from area farmers. “It makes good economic sense, plus southern Ontario can produce some of the best quality and yields of hemp fibre in the world.”
According to Kime, fibre plants like hemp are increasingly used in manufacturing processes as consumers and businesses become more conscious of the environment and recognize the benefits of using renewable resources like bio-fibres. “There is a finite amount of resources like petroleum and minerals, whereas renewable materials like hemp and flax plants can be grown year after year.”
Stemergy operates a 10,000-square-foot facility where plant stalks are processed using proprietary techniques to separate the outer fibre from the inner core of the stalk. “There is a need for materials that are strong but light-weight, particularly in consumer goods,” says Kime. “Composites made from the long, slender fibres on the outside of the plant stalk rival the strength and performance of fibreglass and steel.”
European car makers began using interior parts made from hemp composites in the mid-1990s. With the proven success of those applications, the North American auto industry followed suit a few years later. Today, bio-fibre composites are widely used for interior moulded pieces such as door panels.
There has also been a surge in interest in the construction industry, and a number of Stemergy’s clients use the outer fibre in composites to produce lightweight concrete and other building materials.
The core of the stem has different physical properties, and is primarily processed into chips that can be used as garden mulch, animal bedding and as filler in cement or other construction materials. Stemergy produces and markets 90-litre bags of a hemp core product called HempChips, which it mainly sells to end users.
On the industrial side, Stemergy’s clients range from small shops to large OEMs that supply parts to the automotive sector, both in Canada and the U.S. Since industrial hemp cannot be grown legally in the U.S., Stemergy is ideally situated to supply automotive parts companies in Michigan. For Canadian manufacturers, purchasing commercial quantities of materials from Stemergy is less expensive and complicated than importing it from overseas.
“We have more customers now than we have capacity to supply,” says Kime, noting that the company is in the process of raising capital in order to expand its processing capabilities.
At the same time, Stemergy continues to pursue new markets, including exploring ways to convert waste products into fuel pellets. “There is a strong interest in alternative energy sources” says Kime. “Our research is motivated by market demand.”
Stemergy is also looking at export opportunities in emerging markets like India, China, Pakistan and Asia. “There is an opportunity for Canada to be a world leader in the bio-fibre Industry.”